How to Organize a Production Workshop According to Lean Manufacturing Principles
To optimize a production workshop in line with Lean Manufacturing principles, a structured and methodical approach is essential. Here are the key steps to organizing a production workshop following these effective principles.
Understand the Fundamentals of Lean Manufacturing
Lean Manufacturing aims to maximize operational efficiency while minimizing waste to achieve operational excellence. The LEAN system requires a good organization to ensure efficiency at a lower cost. To organize a LEAN production workshop, it's crucial to understand core concepts, such as, for example, added value (especially through Value Stream Mapping or VSM), waste reduction (Muda), and the importance of continuous improvement (also known as Kaizen). Implementing and adhering to a 5S standard is also fundamental.
Analyze Existing Processes
Before any transformation, thoroughly assessing existing processes is essential. This includes identifying potential sources of waste, such as overstocking, waiting times, and unnecessary movements. This analysis provides a solid foundation for future improvements.
Design an Optimal Layout
The workshop layout plays a crucial role in productivity optimization. Adopting a continuous flow layout, where workstations are logically positioned to minimize movements and promote a smooth flow of materials, is essential. Additionally, clearly delineating different zones with identifiable floor markings is recommended. Industrial adhesive marking tape or adhesive pictograms for floor marking can be effective tools for this purpose.
Engage the Team
On-the-ground employees have a deep understanding of processes and can provide valuable insights for improving efficiency. To bridge the gap between managers and on-site realities, regular Gemba Walks are recommended. Engaging employees is essential for successfully transitioning to a LEAN production workshop. Encouraging team participation in the design and implementation of changes helps them feel like active contributors rather than passive observers.
Implement Visual Management Tools
Lean Manufacturing promotes transparency and effective communication. Using Visual Management tools such as Kanban boards, Key Performance Indicators (KPIs), and Value Stream Mapping (VSM) diagrams makes information easily accessible to everyone in the workshop. This facilitates quick decision-making and rapid problem-solving. For improved information sharing and access, Digital Visual Management, using display screens, is also recommended. Various software solutions, such as SESAHUB, can be used to manage and track KPIs digitally.
Prioritize Flexibility and Adaptability
A LEAN production workshop must be flexible to respond to changes in demand or market conditions. The ability to quickly adjust production based on customer needs while maintaining optimal efficiency is a crucial aspect of Lean Manufacturing.
Foster a Culture of Continuous Improvement
Lean Manufacturing is rooted in the Kaizen principle, encouraging a culture of continuous improvement. Instilling this mindset at all organizational levels is essential, promoting improvement suggestions through feedback forms and iteratively refining processes to continually enhance operations.
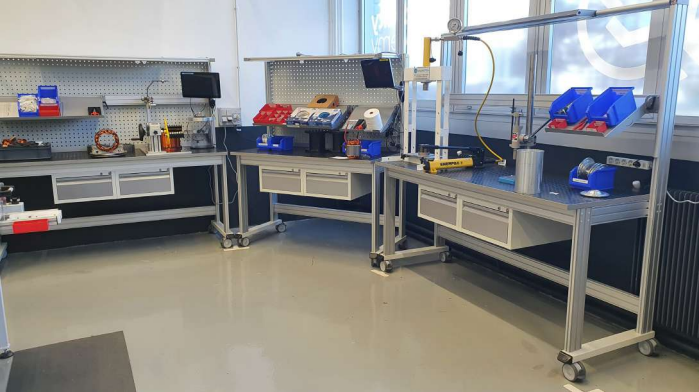
Key Takeaways
Organizing a production workshop according to Lean Manufacturing principles requires a holistic approach. This includes an in-depth analysis of existing processes, a thoughtful layout design, team engagement, the use of Visual Management tools, flexibility, and a culture focused on continuous improvement. By adopting this approach, companies can enhance operational efficiency while reducing waste, resulting in greater competitiveness in the market.